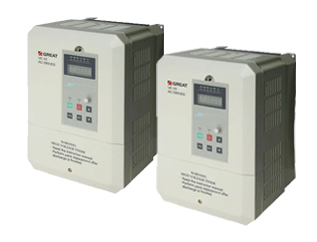
Views:14970
Gelite Inverter Function
![]() |
Inverter integrates high voltage high power transistor technology and electronic control technology, and has been widely used. The function of frequency converter is to change the frequency and amplitude of AC motor power supply, so as to change the period of its motion magnetic field, and achieve the purpose of smoothly controlling motor speed. The emergence of frequency converter simplifies the complex speed control. The combination of frequency converter and AC squirrel cage induction motor replaces most of the original work which can only be done by DC motor, reduces the volume, reduces the maintenance rate and develops the transmission technology to a new stage.
Working Principle of Gelite Inverter
Frequency converter is a power control device that converts power supply into another frequency by using the on-off function of power semiconductor devices. It can realize the functions of soft starting, frequency conversion speed regulation, improving operation accuracy, changing power factor, over-current/over-voltage/over-load protection for AC asynchronous motor. So as to improve the product process, energy saving and environmental protection functions.
Typical Series Introduction of Gelite Inverter
Gelite Frequency Converter Three-phase Universal AC Frequency Converter Speed Regulator-VF-10 Series
|
Performance characteristics: |

Technical specification:
Standard Specification for Gelite Inverter VF10 Series
project |
Standard |
||
Power Supply |
Rated input voltage |
Single-phase 220V, three-phase 220V, 380V, 660V + 20%, 50-60Hz + 5%. |
|
output |
Rated output voltage |
Three-phase 220V, 380V, 660V (maximum output voltage is the same as input power supply voltage) |
|
Quota |
100% continuous |
||
Maximum overload current |
150% 1 minute, 180% 0.2 seconds |
||
control
|
Output Voltage Automatic Adjustment |
When the AVR function is effective, the output voltage is basically unchanged and the constant V/f value is maintained when the input voltage varies. |
|
control mode |
Optimized Space Voltage Vector Control PWM |
||
Frequency control range |
0~400Hz |
||
Output frequency accuracy |
Maximum frequency value (+0.1%) |
||
Output Frequency Resolution |
0.01Hz |
||
Voltage / frequency characteristics |
The rated voltage can be adjusted from 50% to 100%, and the fundamental frequency can be adjusted at 50Hz. |
||
Torque rise |
The 21 way is optional. |
||
Acceleration and deceleration characteristics |
0.1-3600 seconds (up to 36,000 seconds) |
||
Braking torque |
Within 22KW > 20%, over 30KW > 15%. |
||
Frequency setting input |
Keyboard, keyboard potentiometer, 0 ~ 5V, 0 ~ 10V, 4 ~ 20mA and 11 combinations among them, PC serial communication settings, built-in PI regulator |
||
Input command signal |
FWD, REV and 6-way programmable input terminals, 19 functions are optional, such as forward/reverse point motion, multi-segment speed, multi-segment acceleration/deceleration time, free parking, voltage/current switching, etc. |
||
PG signal input |
A+, A-, B+, B-differential input/A-, B-open collector input |
||
Serial communication interface |
RS485/RS232 interface |
||
Standard function |
Current Limit, Torque Lift, Speed Tracking, DC Braking, Power Outage Restart, Slip Compensation, Fault Auto-Reset, Frequency Limit, Bias Frequency, Start Frequency, Jump Frequency, Frequency Gain, Carrier Frequency Adjustment, Acceleration/Deceleration Mode Adjustable, Voltmeter Output, Amperometer Output, Multi-Section Speed, Range Sequential operation, pendulum frequency operation, PI closed-loop operation, proportional linkage, remote control |
||
Protection function |
Overvoltage, undervoltage, overcurrent, current limit, overheat, electronic thermal overload relay, overvoltage stall, data protection |
||
output signal |
The fault relay signal can be programmed open collector output, 14 functions can be selected analog output signal: DC 0~10V or 4~20mA, 4 functions can be selected. |
||
Display |
keyboard |
Parameter setting |
Functional code, data, status |
Operation display |
|||
trouble display |
|||
Conditions of use |
Installation site |
Indoor, no more than 1000 meters above sea level, no dust, no corrosive gas, no direct sunlight |
|
Applicable environment |
- 10 +40 (bare machine is -10 +50), 20%~90% RH (no condensation) |
||
Vibration |
Less than 0.5g |
||
Storage mode |
-25℃~+65℃ |
||
Installation mode |
Wall-mounted, floor-mounted electronic control cabinet |
||
Protection level |
IP20 |
||
Cooling mode |
0.75KW and below are closed self-cooling, others are forced air-cooling. |